
Phosphate
CoatingA phosphate coating is typically used as a pretreatment (primer) that increases overall corrosion protection, lubricity (the friction properties of sliding components) and adhesion of the top coat. Phosphate coatings, along with a top coat of oil are also widely utilized as an interim coating for inventoried and threaded parts to prevent rusting and/or galling.
Phosphate
CoatingA phosphate coating is typically used as a pretreatment (primer) that increases overall corrosion protection, lubricity (the friction properties of sliding components) and adhesion of the top coat. Phosphate coatings, along with a top coat of oil are also widely utilized as an interim coating for inventoried and threaded parts to prevent rusting and/or galling.
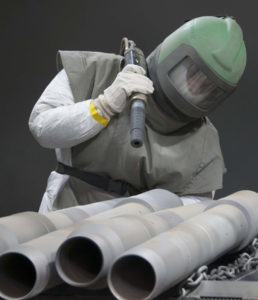
Phosphate coatings improve lubricity.

Photo courtesy of Texas Honing
The phosphating process is a chemical reaction that occurs on an iron base substrate when the part is immersed in the phosphate solution. The primary benefits from phosphate coating are strong adhesion and corrosion protection. There are very few environmental issues relating to the use of phosphate coatings.
HP&C offers two different types of phosphate – Manganese and Zinc. Manganese phosphate coating is softer than zinc phosphate coating and provides superior corrosion and anti-galling properties. Zinc phosphate coating has a larger crystal structure than manganese which provides for better adhesion of various high performance top-coats. Manganese phosphate and zinc phosphate are offered at both its South Houston and Humble facilities.
Responding to increasing requests from clients, HP&C has added a special coating line to provide low weight (150-500-mg/ft2) micro-crystalline zinc phosphate. Phosphate conversion coatings are used on ferrous parts for corrosion resistance, lubrication, or as a foundation for subsequent rust preventatives, coatings or painting, Applied by immersion, the phosphate solution reacts with the surface of the part to form a thin gray layer of micro-crystalline zinc that is aesthetically pleasing and typically does not affect dimensional tolerances. Low weight phosphate tank dimensions are 30”wide x 142”long x 42” deep. Crane capacity is 4,000 pounds.
For additional information on our Electroless Nickel, SBN/QPQ, Phosphate, Spray or other coatings services, please contact your Houston Plating & Coatings sales representative at 713.946.8920.
Houston Plating & Coatings
P.O. Box 418 1301 Georgia
South Houston, TX 77587-0418
Phone: (800) 946-0172 • (713) 946-8920
Fax: (713) 946-8487

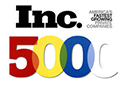
Download Our Brochure
Request a Quote
Houston Plating & Coatings
P.O. Box 418 1301 Georgia
South Houston, TX 77587-0418
Phone: (800) 946-0172 • (713) 946-8920
Fax: (713) 946-8487
Quick Links

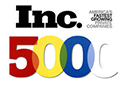